Lithoz- Wie keramische Materialien die Luft- und Raumfahrt revolutionieren
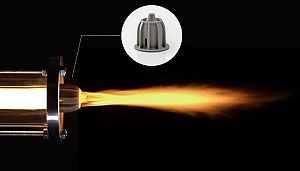
Ein großer und wichtiger Abnehmer des keramischen 3D-Drucks ist die Luft- und Raumfahrtindustrie. Einer der namhaftesten Akteure ist das in Wien ansässige Unternehmen Lithoz, das sich unter anderem auf den keramischen 3D-Druck für den Bereich Aerospace fokussiert hat. Lithoz ist es gelungen, ein Fertigungssystem, das auf dem Lithography-based Ceramic Manufacturing (LCM) basiert, zu entwickeln. Dies erlaubt es, Keramik verstärkt für die Luft- und Raumfahrt einsetzen zu können. Über welche spezifischen Möglichkeiten und Anwendungsbereiche verfügt der keramische 3D-Druck und dessen dafür entwickelte Materialien aber konkret in diesem Fall? Und wie tragen sie dazu bei, die bisherigen Anforderungen der Luft- und Raumfahrt zu verbessern?
Raumschiffe heben mit 3D-gedruckten Keramikteilen ab
Schneller, einfacher und kostengünstiger lautet das Prinzip, das viele Unternehmen und Organisationen im Bereich Aerospace verfolgen. In kaum einem anderen Sektor wie dem der Luft- und Raumfahrt sind die Anforderungen und Erwartungen an additiv gefertigte Teile so hoch. Zu den wohl größten Herausforderungen für dessen Bauteile gehören neben extremen Belastungen auch die Erhitzung und Überhitzung dazu. Besonders die Tatsache, dass sich Turbinenschaufeln mit einer solchen Drehzahl bewegen, dass die damit erzeugte Wärme höher ist als bei der Herstellung des dafür verwendeten Metalls, lässt die herkömmlichen Fertigungsprozesse an ihre Grenzen stoßen. Allerdings müssen die einzelnen Bauteile nicht nur einer übermäßigen Hitze problemlos trotzen können, sondern auch eisiger Kälte. Bedenkt man, dass die Außentemperatur im Weltall schnell einmal auf über – 200 °C fallen kann, wird schnell klar: der Bereich Aersospace benötigt eine zukunftsweisende Alternative für den Herstellungsprozess. Diese unterschiedlichen Extrembedingungen dürfen keinerlei Einfluss auf die Leistung der Teile nehmen, da eine kontinuierliche Stabilität und Porosität unumgänglich in der Raumfahrt sind. Auch die Größe für beispielsweise Katalysatoren spielt in weiterer Folge eine große Rolle: werden die Teile zu groß hergestellt, kann es zu unnötigen Wärmeverlusten führen; bei zu kleinen Teilen kann es zu keiner maximalen Zersetzung des Treibstoffs führen. Das Resultat ist in beiden Fällen eine verminderte Leistung und ein höherer Kostenfaktor. Wie können jedoch durch den keramischen 3D-Druck solche Hindernisse aus dem Weg geschafft werden? Keramik ist für seine Eigenschaften wie der Hitzebeständigkeit, mechanische Leistungen oder auch für die Nutzung zur Herstellung von feinen Bauteilen in höchster Qualität bekannt. Die additive Fertigung ermöglicht daher die Konstruktion komplexer Formen bei gleichzeitiger Reduzierung von Kosten und Vorlaufzeiten – so etwas ist durch die herkömmliche Fertigung nicht möglich. Es lässt sich schnell erschließen, dass der keramische 3D-Druck eine ideale Lösung für eine so anspruchsvolle Branche wie die Luft- und Raumfahrt ist. Lithoz hat sich schnell auf diesem Markt positioniert, indem sie ein Silicium Nitrid (Si3N4) entwickelt haben, das durch seine optimalen Eigenschaften glänzt, wie zum Beispiel enorme Festigkeit selbst bei hohen Temperaturen, ausgezeichneter Beständigkeit bei unerwarteten Temperaturwechseln und auch enorme Härte. Um diese Eigenschaften unter Beweis zu stellen und das Material unter extremen Bedingungen zu testen, hat das österreichische Unternehmen einen Stresstest mit einer aus Si3N4 angefertigten Düse durchgeführt – mit hervorragenden Ergebnissen.
Aerospike-Düse aus Siliziumnitrid: Belastungstest
Das Video wird über Youtube bereitgestellt, dabei wird eine Verbindung zu den Servern von Youtube hergestellt (sh. Datenschutzerklärung).
Das Team von Lithoz wollte die Temperaturwechselbeständigkeit seines Materials anhand der 3D-gedruckte Siliziumnitriddüse testen. Deshalb erhitzten sie diese auf 900 °C und kühlten es anschließend sofort durch Wasserabschrecken auf Raumtemperatur ab. Trotz der hohen thermischen Belastung überstand die Düse aus dem 3D-Drucker den Test ohne jegliche Schäden. Laut Lithoz hält das Material sogar eine höhere Temperatur als 900 °C aus.
Was bedeutet das nun konkret für die Luft- und Raumfahrt? Mittels additiver Fertigung durch Verwendung von Silicium Nitrid besteht für die 3D-gedruckten Teile eine hohe Thermoschockbeständigkeit, wie auch eine enorme Festigkeit, Zähigkeit und der Vorteil, dass komplexe keramische Bauteile hergestellt werden können. Beispielsweise werden dadurch für den Bereich der Raumfahrt speziell Mikroturbinen, Laufräder und Schneidwerkzeuge rasch und präzise hergestellt und bei einer Temperatur von bis zu 1200 °C eingesetzt werden, die in einem traditionellen Produktionsprozess einen hohen Zeit- und Kostenanspruch hätten. Si3N4 findet aber auch in anderen Industrien eine weitreichende Verwendung: der medizinische Bereich profitiert von dem Material besonders durch seine antibakterielle und antivirale Oberflächenchemie, wie auch durch seine hervorragende Biokompatibilität. Konkret eignet sich Silicium Nitrid vor allem für die Bereiche der Zahnmedizin, Orthopädie und kraniomaxillofaziale Implantate. Auch im Kampf gegen das Coronavirus ist Siliciumnitrid optimal einsetzbar, denn durch seine Oberflächenbeschaffenheit ist es resistent gegenüber Viren und Bakterien.
3D-Druck auf dem Mond: Fakt oder Fiktion?
Vielleicht klingt es wie aus dem Drehbuch eines Sci-Fi Films, aber die Verwendung von Mondstaub oder auch Moondust genannt, wird bereits mittels keramischen 3D-Druck bei Lithoz verwendet. Ob das wohl der nächste Schritt in Richtung menschlichen Lebens im Weltraum ist? Eines ist auf jeden Fall sicher: durch die LCM-Technologie ist es möglich, dass Bauteile für den Aerospace Bereich aus Mondregolith in hochpräziser Abmessung hergestellt werden können. Das heißt für zukünftige Missionen in Richtung Weltall, dass nötige Ersatzteile und Werkzeuge vor Ort und auf Abruf herstellbar sind. Für die Nutzung der Ressource vom Mond, die als ausreichend verfügbar und ungiftig für den Menschen gilt, mittels keramischen 3D-Druck, müssen einige Schritte beachtet werden. Besonders die enge Projektarbeit mit der Europäischen Weltraumorganisation (ESA) ermöglicht eine kontinuierliche Erforschung und Weiterentwicklung des Mondstaubs in Hinblick auf den 3D-Druck. Hierbei wurde im Zuge des EU Horizon 2020 Projekts RHEFORM bereits an einer Lösung zum Ersatz von Hydrazin geforscht. Der als krebserregende geltende Stoff spielt in der Raumfahrt bereits seit den 1960er Jahren eine große Rolle. Durch den Einsatz des 3D-Druckers CeraFab 7500, ein DLP (Digital Light Processing)-basiertes additives Fertigungssystem der Firma Lithoz wie auch ihr selbstentwickeltes photohärtbares Bindemittel, das seine Anwendung in diesem Projekt fand, konnten die Forscher einen bedeutsamen Fortschritt bezüglich verbesserter Anwendungen im Raumfahrtbereich erzielen. Um die weiteren Möglichkeiten von Moondust erforschen zu können, laufen auch derzeit einige Projekte, an denen Lithoz maßgeblich beteiligt ist.
Leichtere Produktion von Flugzeugturbinen dank Lithoz
Damit es Flugzeugen überhaupt erst ermöglicht wird abzuheben, sind allen voran die Turbinen ausschlaggebend für jeden Flug. Eines der wohl wichtigsten Teile innerhalb der Turbine sind die Turbinenschaufeln, die auf traditionelle Art im Feingussverfahren hergestellt werden. Hier eröffnet sich allerdings eine schwerwiegende Problematik: bei herkömmlichen spritzgegossenen Kernen begrenzt sich die Möglichkeit zur Einarbeitung von mehrflügeligen, komplexen und engen Kühlelementen. Die Folgen können auf lange Sicht nicht nur kostspielig sein, sondern auch Sicherheitsrisiken mit sich bringen. Wie können Turbinen heutzutage effizienter und innovativer hergestellt werden, ohne dass es einen Kostenanstieg gibt? Die Lösung bietet das eigens 450, ein Material auf Siliziumdioxidbasis, das sich hervorragend für die Herstellung von Gusskernen mittels LCM-Technologie eignet. Durch eine geringe thermische Ausdehnung und einer sehr hohen Porosität ist das Material optimal für die additive Herstellung von präzisen Keramikkernen mit filigranen Details für die Luftfahrt geeignet. Die Werkzeuglose Herstellungsmethode durch die additive Fertigung verhindert nicht nur hohe Kosten und einen enormen Mehraufwand, darüber hinaus ermöglicht die LCM-Technologie eine schnellere Produktion. Demnach können sowohl Prototypen und wie auch Serienproduktionen in kurzerhand angefertigt werden und somit eine offensichtlich kürzere Markteinführungszeit in Anspruch nehmen. Die Gusskerne können selbst bei komplexen Formen mit Merkmalen wie beispielsweise Hinterkanten eine Feinheit von mindestens 200 µm aufweisen und eine Größe von bis zu 30 cm annehmen. Mit dem unternehmenseigenen CeraFab System gelang es Lithoz sogar, mehrere Gusskerne mit einer Größe von 500 mm herzustellen – das gab es in dieser Form zuvor noch nicht und zeigt damit zukunftsweisende Lösungen für die Herstellung von Prototypen bis hin zu großen Kernen für industrielle Turbinen durch Lithoz.
Die neuesten von Lithoz entwickelten Materialien
Während die vorhergegangenen Materialien bereits durch ihre jahrelange Verwendung erprobt sind, erweitert sich die Auswahl an keramischen Materialien durch Lithoz um zwei weitere. Zum einen bietet Silizium-Infiltriertes Siliziumkarbid (SiSiC) als leichtes, aber gleichzeitig hartes keramisches Material eine sehr gute Wärmeleitfähigkeit und minimale Wärmeausdehnung. SiSiC-Keramiken werden dahingehend oft als Wärmetauscher, Düsen oder als Endstücke für unterschiedliche Arten von Brennern verwendet. Auf der anderen Seite steht Aluminiumnitrid (AIN), das mittels DLP-basierter Fertigungstechnik entwickelt wird. Wie auch bei SiSiC verfügt das Aluminiumnitrid über eine hohe thermische Wärmeleitfähigkeit. Die Biegefestigkeit von AIN, die während der Forschungsproben gemessen werden konnte, schwankte hingegen zwischen 320 und 498 MPa. Diese Eigenschaften tragen in Summe dazu bei, dass somit die Herstellung von hochkomplexen und rissfreien Teilen möglich wird und schafft dadurch neue Anwendungsmöglichkeiten im Bereich des Wärmemanagements.
Diese große und diverse Bandbreite an verschiedenen Materialien und Entwicklungen verdeutlichen sehr stark, wie weit der keramische 3D-Druck im Bereich der Luft- und Raumfahrt bereits fortgeschritten ist und welche neuen Möglichkeiten sich dadurch eröffnen. Neben der Herstellung von Bauteilen mit immens komplexen Strukturen ermöglicht Lithoz mit seinen Materialien ebenfalls eine große Designfreiheit, verbunden mit höchster Präzision. Unabhängig davon, ob das 3D-gedruckte Teil nur einige Millimeter oder einen halben Meter groß sein soll, durch die erstklassige Materialqualität und die konstante, pixelgenaue Belichtungspräzision, die bei der Nutzung eines CeraFab Systems gleichmäßig über die komplette Bauplattform erzielt wird, ist auch die Anfertigung von Teilen einer Serienproduktion endlich kein Problem mehr.
An welchen Projekten arbeitet Lithoz aktuell im Aerospace Bereich?
Verschiedene Projekte, an denen Lithoz wesentlich beteiligt ist, intensivieren dies noch zusätzlich: gemeinsam mit Forschenden der Universität Poitiers (Frankreich), der FOTEC Forschungs- und Technologietransfer GmbH (Österreich) und der Fachhochschule Wiener Neustadt GmbH (Österreich) hat Lithoz den Vergleich von gedruckten monolithischen Keramikkatalysatoren mit traditionell hergestellten Katalysatoren wie auch mit verschiedenen Washcoat-Schichten präsentiert. Mit Hinblick auf die Zersetzung von hochkonzentriertem Wasserstoffperoxid konnte dadurch festgehalten werden, dass besonders der Faktor der Porosität im direkten Vergleich einen großen Unterschied macht. Im Allgemeinen ist die gemessene Porosität der gedruckten Struktur immens größer als bei extrudierter Struktur. Dies hat unter anderem als Folge, dass bei einer höheren Porosität auch das instationäre Temperaturverhalten verbessert wird. Diese Ergebnisse können weitere entscheidende Schritte für die verstärkte Nutzung des keramischen 3D-Drucks in der Luft- und Raumfahrt sein.