Lithoz- How ceramic materials are revolutionising aerospace
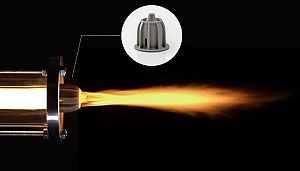
A large and important customer of ceramic 3D printing is the aerospace industry. One of the most notable players is the Vienna-based company Lithoz, which has focused on ceramic 3D printing for the aerospace sector, among other things. Lithoz has succeeded in developing a manufacturing system based on Lithography-based Ceramic Manufacturing (LCM). This makes it possible to increasingly use ceramics for aerospace applications. But what specific possibilities and areas of application does ceramic 3D printing and the materials developed for it have in this case? And how do they contribute to improving the current requirements of aerospace?
Spacecraft take off with 3D-printed ceramic parts
Faster, simpler and cheaper is the principle that many companies and organisations in the aerospace sector follow. In hardly any other sector like aerospace are the requirements and expectations for additively manufactured parts as high. Probably the greatest challenges for its components include extreme loads as well as heating and overheating. In particular, the fact that turbine blades move at such a speed that the heat generated by them is higher than that generated by the metal used for their manufacture means that conventional manufacturing processes are pushed to their limits. However, the individual components must not only be able to withstand excessive heat without problems, but also freezing cold. Considering that the outside temperature in space can quickly drop to over - 200 °C, it quickly becomes clear: the aerospace sector needs a forward-looking alternative for the manufacturing process. These different extreme conditions must not have any influence on the performance of the parts, as continuous stability and porosity are indispensable in space travel. The size for catalysts, for example, also plays a major role downstream: if the parts are manufactured too large, it can lead to unnecessary heat loss; if the parts are too small, it can lead to no maximum decomposition of the propellant. The result in both cases is reduced performance and a higher cost factor. But how can ceramic 3D printing remove such obstacles? Ceramics are known for their properties such as heat resistance, mechanical performance, and also for their use in producing fine components of the highest quality. Additive manufacturing therefore enables the design of complex shapes while reducing costs and lead times - something that is not possible through conventional manufacturing. It can be quickly deduced that ceramic 3D printing is an ideal solution for an industry as demanding as aerospace. Lithoz has quickly positioned itself in this market by developing a silicon nitride (Si3N4) that shines with its optimal properties, such as enormous strength even at high temperatures, excellent resistance to unexpected temperature changes and also enormous hardness. To prove these properties and to test the material under extreme conditions, the Austrian company carried out a stress test with a nozzle made of Si3N4 - with excellent results.
Silicon nitride aerospike nozzle: stress test
The video is provided via Youtube , a connection to the servers of Youtube is established (see privacy policy).
The Lithoz team wanted to test the thermal shock resistance of its material using the 3D-printed silicon nitride nozzle. Therefore, they heated it to 900 °C and then immediately cooled it down to room temperature by quenching it with water. Despite the high thermal stress, the 3D-printed nozzle survived the test without any damage. According to Lithoz, the material can even withstand a higher temperature than 900 °C.
So what does this mean in concrete terms for aerospace? By means of additive manufacturing using silicon nitride, the 3D-printed parts have a high thermal shock resistance, as well as enormous strength, toughness and the advantage that complex ceramic components can be produced. For example, for the aerospace sector, this means that micro-turbines, impellers and cutting tools in particular can be produced quickly and precisely and used at temperatures of up to 1200 °C, which would take a long time and be very expensive in a traditional production process. However, Si3N4 is also widely used in other industries: the medical field benefits from the material especially due to its antibacterial and antiviral surface chemistry, as well as its excellent biocompatibility. Specifically, silicon nitride is particularly suitable for the fields of dentistry, orthopaedics and craniomaxillofacial implants. Silicon nitride can also be optimally used in the fight against the coronavirus, because its surface properties make it resistant to viruses and bacteria.
3D printing on the moon: fact or fiction?
It may sound like something out of the script of a sci-fi movie, but the use of lunar dust, or moondust, is already being used via ceramic 3D printing at Lithoz. I wonder if this is the next step towards human life in space? One thing is for sure: LCM technology makes it possible to produce aerospace components from lunar regolith in highly precise dimensions. For future space missions, this means that the necessary spare parts and tools can be produced on site and on demand. For the use of the resource from the moon, which is considered to be sufficiently available and non-toxic for humans, by means of ceramic 3D printing, some steps have to be taken into account. Especially the close project work with the European Space Agency (ESA) enables continuous research and further development of lunar dust with regard to 3D printing. In the course of the EU Horizon 2020 project RHEFORM, research has already been carried out on a solution to replace hydrazine. The substance, which is considered carcinogenic, has played a major role in space travel since the 1960s. By using the CeraFab 7500 3D printer, a DLP (Digital Light Processing)-based additive manufacturing system from Lithoz, as well as their self-developed photocurable binder, which found its application in this project, the researchers were able to achieve significant progress in terms of improved applications in the space sector. In order to be able to explore the further possibilities of Moondust, several projects in which Lithoz is significantly involved are also currently underway.
Lighter production of aircraft turbines thanks to Lithoz
Turbines are the most important part of an aircraft's ability to take off. One of the most important parts inside the turbine are the turbine blades, which are traditionally produced by investment casting. Here, however, a serious problem arises: with conventional injection-moulded cores, the possibility of incorporating multi-bladed, complex and narrow cooling elements is limited. In the long run, the consequences can not only be costly but also entail safety risks. How can turbines be manufactured more efficiently and innovatively these days without increasing costs? The solution is offered by the proprietary 450, a silica-based material that is ideally suited for the production of cast cores using LCM technology. Due to a low thermal expansion and a very high porosity, the material is ideally suited for the additive manufacturing of precise ceramic cores with filigree details for aerospace applications. The tool-free manufacturing method through additive manufacturing not only avoids high costs and enormous additional effort, but LCM technology also enables faster production. Accordingly, prototypes as well as series productions can be made in a short time and thus have an obviously shorter time to market. The casting cores can have a fineness of at least 200 µm even for complex shapes with features such as trailing edges and can take on a size of up to 30 cm. With the company's own CeraFab system, Lithoz was even able to produce several cast cores with a size of 500 mm - this had not been done before in this form and thus demonstrates forward-looking solutions for the production of prototypes up to large cores for industrial turbines by Lithoz.
The latest materials developed by Lithoz
While the previous materials are already proven through their years of use, Lithoz adds two more to the range of ceramic materials. Firstly, Silicon-Infiltrated Silicon Carbide (SiSiC), a lightweight yet hard ceramic material, offers very good thermal conductivity and minimal thermal expansion. SiSiC ceramics are therefore often used as heat exchangers, nozzles or end pieces for different types of burners. On the other hand, there is aluminium nitride (AIN), which is developed using DLP-based manufacturing technology. As with SiSiC, the aluminium nitride has a high thermal conductivity. The bending strength of AIN, on the other hand, which could be measured during the research samples, varied between 320 and 498 MPa. Together, these properties contribute to the possibility of producing highly complex and crack-free parts, thus creating new applications in the field of thermal management.
This large and diverse range of different materials and developments illustrates very clearly how far ceramic 3D printing has already advanced in the aerospace sector and what new possibilities it opens up. In addition to the production of components with immensely complex structures, Lithoz also enables great design freedom with its materials, combined with the highest precision. Regardless of whether the 3D-printed part is to be just a few millimetres or half a metre in size, the first-class material quality and the constant, pixel-precise exposure precision achieved by using a CeraFab system evenly across the entire build platform means that the production of parts for series production is finally no longer a problem.
What projects is Lithoz currently working on in the aerospace sector?
Various projects, in which Lithoz is substantially involved, intensify this even more: together with researchers from the University of Poitiers (France), FOTEC Forschungs- und Technologietransfer GmbH (Austria) and the University of Applied Sciences Wiener Neustadt GmbH (Austria), Lithoz has presented the comparison of printed monolithic ceramic catalysts with traditionally produced catalysts as well as with different washcoat layers. With regard to the decomposition of highly concentrated hydrogen peroxide, it could be determined that especially the factor of porosity makes a big difference in direct comparison. In general, the measured porosity of the printed structure is immensely greater than that of the extruded structure. One of the consequences of this is that the transient temperature behaviour is also improved with a higher porosity. These results can be further decisive steps for the increased use of ceramic 3D printing in aerospace.