Aerospace Team Graz
Introducing the Aerospace Team Graz
Our main focus is to develop rockets for international competitions such as the European Rocketry Challenge (EuRoC). Furthermore, we test and build various propulsion systems and small-scale satellites.
We get hands-on experience by researching and developing most components of our projects by ourselves. Our association is a great way to complement your studies and gives many opportunities to write a bachelor or master thesis.
Our rockets are a team effort. It is a great environment for practicing soft skills and leadership competence. By connecting like-minded people and companies, we want to extend our network to the international aerospace sector.
Projects
CubeSat Challenge
In order to pass on our enthusiasm for technology and space travel, we created the CubeSat Challenge. Here, high school students have the opportunity to plan and implement their own mini-satellite. The CubeSat can be implemented in the course of a diploma thesis or VWA.
The challenge provides great framework conditions for exciting experiments. The winners of our challenge then have the opportunity to integrate their CubeSat into our rocket as a payload and test it under real conditions during the flight at the EuRoC.
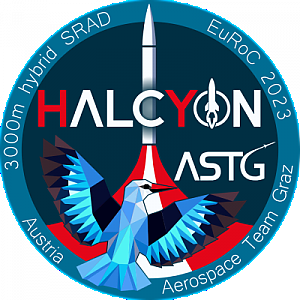
Halcyon
Halcyon is a new competition rocket for the European Rocketry Challenge 2023. Competition category: 3km hybrid SRAD (student researched and developed).
The exciting part of the new project is the first use of a hybrid propulsion system, which the team has already been working on for several years in the course of the testbed Penguin. Both the propulsion system and the filling system are completely self-designed.
Nitrogen is fed from a high-pressure tank (300 bar) into the load-bearing oxidizer tank to pressurize it at a constant pressure. The oxidizer, nitrous oxide, is then injected into the combustion chamber via a swirl injector. The solid component is located in the combustion chamber and consists largely of paraffin wax.
The Aerostructure module is responsible for the integration and construction of the tanks, as well as for the stability of the rocket. For data recording and analysis, Avionics uses an advanced version of the AVES II hardware and software. The telemetry system is also being revised for Halcyon and equipped with new hardware and software.
For a safe landing, our two-parachute system, at the top of the rocket, is being redesigned and verified with our homemade test setup, Frieda. Frieda contains sensors to obtain altitude, acceleration and position data and will be used in drop tests. Halcyon should be able to carry a payload of 4 kg in the form of 3 U CubeSats for flight. For the development of the minisatellites, the previous projects will be continued and students from Austrian high school classes will be cooperated with.
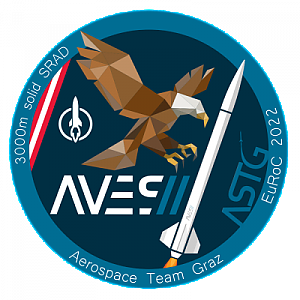
AVESII
Designed for the 3km solid SRAD category at the European Rocketry Challenge in Portugal, AVES II retains the "Student Researched and Developed" philosophy and builds on the knowledge and success of its predecessor AVES I.
The payload consists of three 1U CubeSats. Two of which were developed entirely by HTL students. We will continue to share our enthusiasm for rocket technology with the next generation and keep up the successful cooperation that started last year.
Directly below the nosecone is the recovery module, which consists of a two-stage deployment system and relies on a main and a drogue parachute.
One compartment further is the avionics bay – the brain of the rocket. It includes the power supply, the telemetry system (antennas), the camera system, the black box and of course the flight computer, which was designed and manufactured in-house. The core works with an improved version of the self-developed real-time operating system RavenOS.
Avionics Bay Assembly
The video is provided via Youtube , a connection to the servers of Youtube is established (see privacy policy).
Separated from the avionics module by a void volume, the air brake provides more precise control to reach our target altitude of 3 km.
Air Brake Assembly
The video is provided via Youtube , a connection to the servers of Youtube is established (see privacy policy).
Our solid rocket engine again consists of Rocket Candy (a mixture of potassium nitrate and sorbitol, KNSB) but it has been greatly improved over its predecessor and is therefore one of the highlights of AVES II. New processes and geometries enable more efficient casting and more precise thrust of the solid propellant. In addition, a special sensor system at the top of the booster allows the combustion process to be monitored.
Engine Assembly
The video is provided via Youtube , a connection to the servers of Youtube is established (see privacy policy).
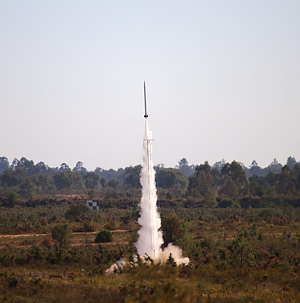
All the subsystems mentioned are enclosed in a structural load-bearing housing made of fiber composites, largely carbon.
To ensure communication with the self-developed ground station, glass fiber was used in the radio-permeable areas.
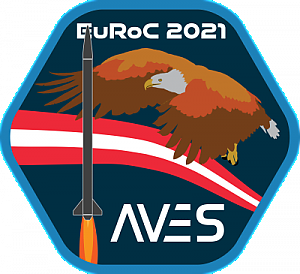
AVES
AVES was developed as a competition rocket for the European Rocketry Challenge (October 2021, Portugal).
We developed our own solid propellant from potassium nitrate and sorbitol (KNSB), designed to reach an altitude of 3000m. The braking system, which was also specially designed, served to reach the required target height precisely. The flight computer, which controls all the electronics in the rocket, including its own operating system and associated hardware, was developed by our Avionics Module.
The Nosecone contains a payload with the form factor 3U CanSat. To continue our passion for rocket development, the content of the payloads was created in collaboration with students from higher technical schools. They were given a free choice in the function of the mini-satellites. A wide variety of sensors in the payload are used to collect data about the rocket's flight behavior. In order to land AVES safely, a self-designed two-parachute system is used.
Designing, manufacturing & testing - AVES competition rocket
The video is provided via Youtube , a connection to the servers of Youtube is established (see privacy policy).
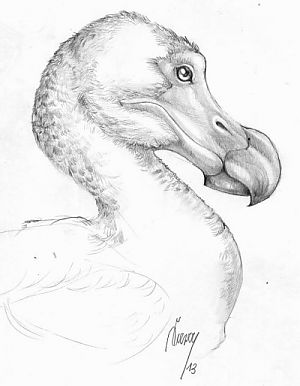
Dodo (Prototype)
Project DODO is a rocket prototype and the first rocket developed by the association. The mission: to gather initial experience with the technical challenges of rocket construction and to overcome the organizational hurdles of a new team.
Due to delays in production, in favor of AVES I, all of the team's capacity was put into developing the competition rocket, which meant DODO, named after a flightless bird, never took off - a self-fulfilling prophecy.
Nevertheless, the experience gained by the team was essential for the rapid implementation of AVES.
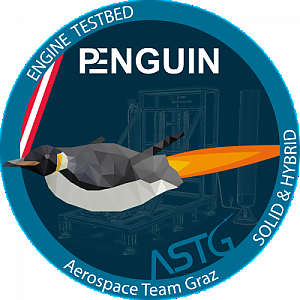
Penguin
Penguin is our self-developed modular test stand for our various engine tests. Penguin consists of a variable construction made of aluminium profiles, integrated measuring, and safety systems, and is also fully automated. Both the solid engines of AVES I & II and the new hybrid engine were tested and developed with this test stand. Penguin can be converted quickly and easily without having to compromise on safety. The data obtained can be directly evaluated and verified. Since our flight computer is also compatible with the integrated electronics, both its hardware and software can be tested directly.